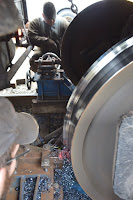 |
Cutting heads in position. |
The Museum's high hood Alco model HH660 locomotive received its first restorative work this week when Scott Hutton - with able assistance from Josh Kiavo - was on hand to turn the wheels. The last operating assignment for the 125 was switching grain cars at the Port of Longview. In this intensive use, the tapered profile of the steel wheels wore down into a hollow.
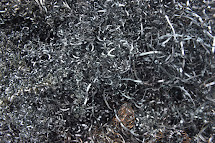 |
The wheel lathe produced many shavings and chips. |
This model HH660 was built by the American Locomotive Company for the Northern Pacific Railway in 1940, and was the first diesel electric switcher that road brought to Seattle. It later served the Walla Walla Valley Railway and RELCO locomotive leasing before it was purchased by the Port of Longview. It was retired in 2004 and in November 2021 moved to Snoqualmie after years of offsite storage; evaluations of the locomotive and its systems are ongoing. 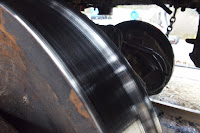 |
Wheel profile detail. |
The steel wheels were worn beyond acceptable limits and Scott's portable wheel lathe was summoned to bring the tread back into profile. Wheel profiles are important for maintaining adhesion (avoiding wheel slip), minimizing friction, reducing wear, minimizing hunting (undesired side to side motion) and providing a smooth ride. The profile used on the 125 was developed by the American Association of Railroads and features a 1:20 tread taper.
 |
Completed wheel. |
Turning a new profile onto a wheel usually involves removing the offending wheel sets from the car or locomotive and placing them in a wheel lathe. Scott has a set of portable cutter heads that allow a locomotive wheel set to be profiled in situ. How is that possible? By using the locomotive's electric traction motors to turn the wheels. Each axle and wheel set is addressed individually by jacking up the motor and axle and powering the motor with an electric welding outfit. The output of the welder is modulated until the axle is spinning at a rate appropriate for the carbide cutters. A thin sliver of steel is peeled off; it takes a full work day to profile each wheel set, and care must be used to ensure the diameter of both wheels is the same.Check out this short video illustrating the process:
3 comments:
Neat to see this process!
Dan
Hey, the Southern Pacific did something similar in reprofiling wheel treads on steam locomotives......they would pull the locomotive (and tender) back and forth on a short track, attached with cables to a machine they called a Lidgerwood - the cutting blade fastened to the brake hanger of the driver being retreaded.
Robert
Great work, Scott & Josh. It's exciting to see those wheels turning under their own motors. Did you use the diesel engine to generate electrical power?
Post a Comment